APR RECOGNIZES HUSKY’S LATEST DEVELOPMENT OF LIGHT-WEIGHT RECYCLABLE CSD BARRIER PACKAGING
Husky’s continued collaboration with Mitsubishi Gas Chemical has led to a significant evolution of our fully recyclable Multi-Layer PET solution for small-format carbonated soft drinks (CSD), which has now earned recognition from the Association of Plastic Recyclers (APR) for 3.3% MXD6 integration!
Building on our 2020 APR accreditation for 2.5% MXD6, this new milestone enables us to lightweight single-serve CSD bottles, starting at just 12g. The key is the incorporation of high-barrier material in a fully recyclable package, enabling us to significantly reduce the required PET resin.
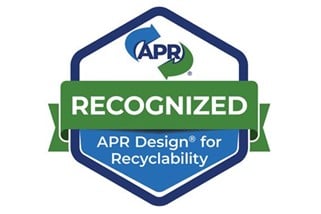
Our continued evolution of the solution enables the application of the technology to a broader range of bottle sizes, addressing the demands of beverage packaging producers for recyclable barrier packaging across various application formats.
Based in North America, the APR is the gold standard for recyclability and is referenced by leading organizations around the world. Their recognition underscores our commitment to sustainable practices and processes, which enables our customers to optimize operations, increase design circularity, and reduce costs.
Unlocking the Potential of PET for Small-Format CSD Packaging
For years, PET has been the top choice for CSD packages ranging from 356 to 600ml due to its strength, clear appearance, see-through nature, and eco-friendly profile. However, when it comes to packages of 355ml and smaller, the permeability of PET allows CO₂ to escape, leading to a shorter product shelf life. Traditionally, maintaining reasonable shelf-life required monolayer bottles to be thick and heavy, which has both economical and sustainability implications. Another option is to enhance barrier performance by adding polymers like nylon, which can reduce CO₂ egress, but typical incorporation processes pose a significant issue by impacting PET recycling streams.
Aluminum cans are therefore often preferred for smaller sizes. However, they come with their own challenges, including limited resources, increased material costs, and a larger carbon footprint compared to PET.
At Husky, we have long recognized the need for a solution that balances both performance and sustainability requirements, which made it clear that a new approach for small-format CSD packages was imperative.
Husky’s Innovative Solution for Small-Format CSD
The first iteration of our groundbreaking Multi-Layer package incorporated up to 2.5% MXD6, which was ideal for bottles heavier than 16 grams. This new breakthrough (up to 3.3% MXD6) expands our scope, enabling us to cater to bottles as light as 12 grams, significantly broadening the reach of sustainable packaging solutions.
Some of the highlights of our groundbreaking multi-layer package include:
Newly engineered barrier material for CO₂ retention: Mitsubishi Gas Chemical’s M6000 series barrier material is specially engineered for CO₂ retention, good mechanical performance, and easy separation from PET in traditional recycling equipment.
Precision-injected barrier material: Our latest innovation is based on the precise injection of barrier material into bottle sidewalls, optimizing the amount of MXD6 while maintaining the barrier effectiveness.
Full recyclability: Our Multi-Layer package remains fully recyclable during conventional post-consumer processing, aligning with sustainability and circular economy goals.
Cost-effective, lightweighting initiatives: By incorporating a high-barrier material, our solution enables a reduction of PET resin usage, leading to substantial cost savings without compromising on performance.
Husky’s Sustainable Multi-Layer Technology
Husky's Multi-Layer equipment is based on a high-precision co-injection process, which sandwiches a functional component between two PET layers. Husky’s accurate layer control provides unlimited freedom in selecting the amount, thickness and placement of the functional material.
Husky co-injection systems are based on the HyPET®HPP5e family of systems, which are designed for maximizing production output, while reducing part variability, and increasing part quality.
Reach out to our team of PET experts to learn more about how we can enable you to optimize operations, increase design flexibility, and reduce costs.