热流道在优化系统平衡中所起的关键作用
平衡性对于注塑工艺的优化而言,有着重要的影响;有时往往也是验证中的一个限制因素。对于凭借尽可能宽泛的加工窗口力求生产无飞边、充分填充、尺寸一致的部件的加工商来说,平衡性起着主导作用。平衡性是对某个特定模具固有变化的数字性表述,通常通过比较最重和最轻部件之间的差异来衡量。平衡性量测的目标之一是尽力减小这种差异变化,而热流道在这方面则有着显著的影响。
本文将探讨系统和热流道平衡的工艺基础及其对于模具认证的影响。我们将聚焦那些有助于开发设计精良的热流道的相关因素,以及造成系统不平衡的原因。我们还将研究影响几何体熔体通道平衡之外的短射(注射不足)平衡性的因素,以及如何测量系统平衡性,如何基于特定的最终用途应用而设定期望。
为何要担心平衡性?
注塑成型中的型腔平衡是模具验证过程中所要考量的若干基准指标之一。在成型工艺的评估中,热流道可以辅助微调平衡性。虽然有许多信息资源,如网站和出版物,专门讨论平衡的重要性,但就哪些因素组成了“可接受的”平衡性,其相关信息却少之又少亦或完全没有。针对最为有效的平衡性量测程序,其广为大众所认可的信息同样缺失。
对于许多行业观察家来说,系统平衡性究竟指代什么尚不明确。它是否突出各型腔之间的差异,或者需要多少容量来填充模具?围绕着注塑平衡性的定义,仍缺乏清晰的概念,因为这些规定皆由使用者自己来解读,因而在本质上是主观的。
使用多型腔模具进行注塑操作时,为了拥有最大的潜在工艺窗口,所有模腔应同时填充。各型腔之间以及各个注射点之间的差异,令高度一致地模塑尺寸统一的部件变得极为困难。
模塑部件的不一致性可以多种不同的缺陷形式得以呈现。显然,部件不一致的情况绝非人们所愿,而这些差异所造成的真正影响又有哪些?不一致性意味着:如果所需的规格无法达成,则不得不延长认证时间。质量差往往导致成本的增加,可以表现为报废率升高、额外的检查和保修费用激增。部件之间的差异性也会对制造合格部件的工艺窗口加以限制,最终降低灵活度和工艺的稳健性。
这些结果都是“水线之上”的,可以直接测量。不一致的部件还有多重“水线之下”的成本。这些“隐形成本”可以是更高的风险、加速处理、缓冲库存(安全库存)、销售损失、难以预测的盈亏、客户忠诚度下降和更高的管理成本。通过竭力减少差异性,加工商可以创建更强有力的模塑系统和模具,能在指定的规格范围内生产更多更好的部件。
解决热流道系统的不平衡性
短射(注射不足)平衡性受到很多外在因素的影响:
- 注塑机(吨位、压板状况、螺杆设计)
- 树脂(类型、品质、制备)
- 加工工艺(注射剖面,冷却时间,注射量)
- 模具(模具类型、排气、冷却布局、刚度、部件的几何形状)
热流道系统也有影响短射(注射不足)平衡性的诸多因素。热流道的关键考量因素包括熔体通道布局、加热器布局、推板螺栓连接和推板冷却。其它影响因素包括浇口方式、驱动和温度控制。
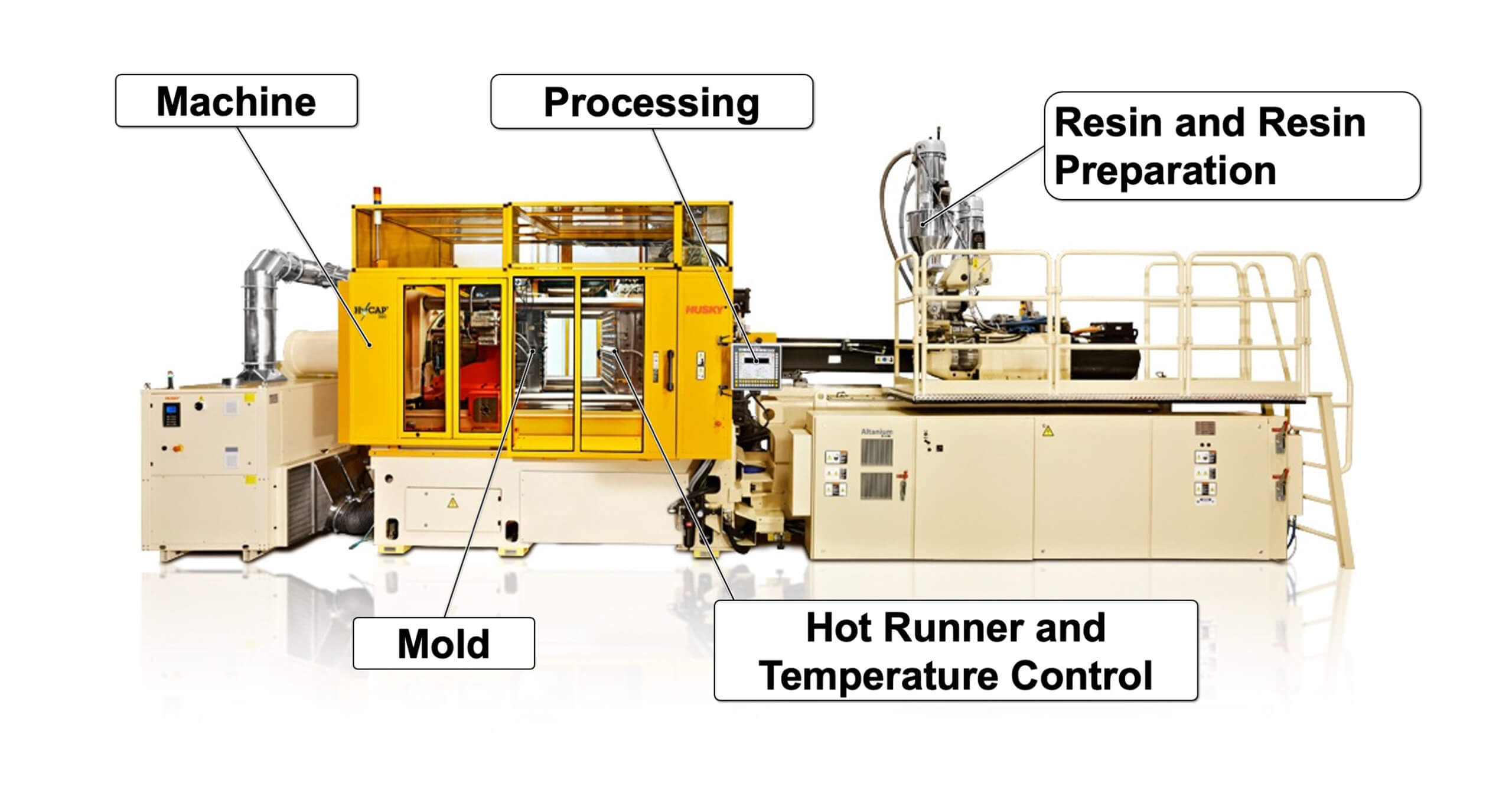
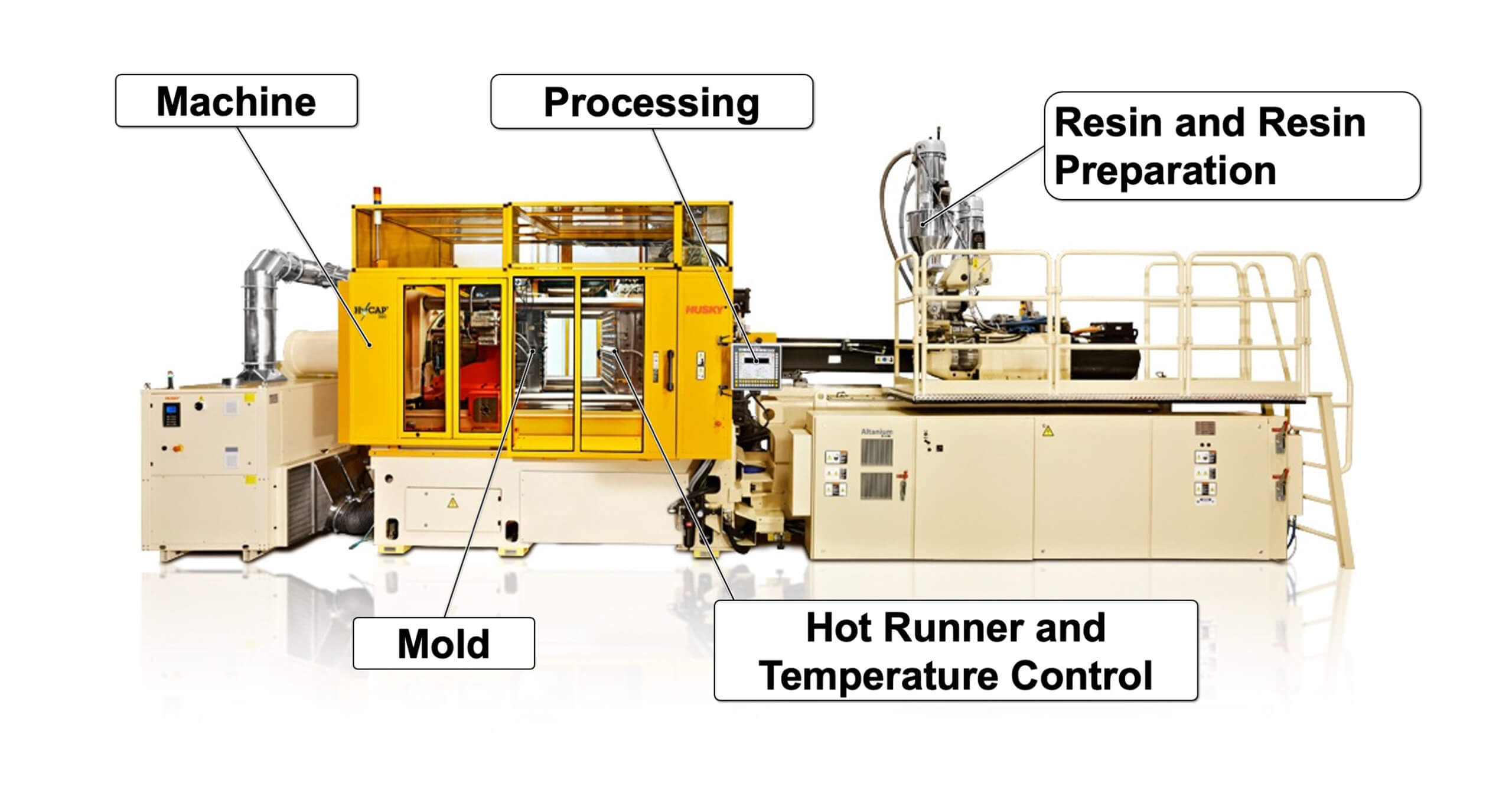
简单地将树脂由PC/ABS更换为聚丙烯树脂,多型腔模具的平衡性由65%提高到93%。在不对模具型腔和热流道作出任何改变的情况下实现这一提升,说明了树脂类型会对短射(注射不足)平衡性产生很大影响。伴随温度或剪切所发生的些许变化,一些树脂的粘度会产生显著的变化。树脂与工艺和模具条件的相互作用不尽相同,往往取决于树脂的属性。基于不同的树脂和模具,其对平衡性的影响可能是正面的,亦有可能是负面的。
虽然热流道可以为模塑商提供显著的优势,但它们却增加了模具的复杂性,也可能导致填充不平衡。当需要模塑的型腔多于一个以上时,就可能存在平衡问题。所有的浇口性能表现一致,这一点极为重要。在为要求严苛的终端市场(例如医疗和保健)模塑公差要求极严或薄壁部件时尤甚。如果浇口的运行方式不保持一致,模具平衡性则被打破。短射(注射不足)平衡性的重点在于:塑料的注射量小于制造填充完全且尺寸稳定的部件所需的用量。
阀杆时序也会对短射(注射不足)平衡性产生重大影响。在一个32腔注射器针筒模具中,凭借UltraSync®推板驱动技术将阀杆驱动从单点独立气动活塞控制改为同步所有阀杆,将短射(注射不足)平衡性从60%提高至90%。
热力均匀令填充更趋平衡
热流道的目标是将熔体输送到模具的每一个型腔,通过设计优化,热流道的温度曲线也能影响平衡性。理想情况下,无论流动路径如何,树脂的热度情况均保持一致。影响温度变化的几个因素包括加热器技术、注射点布局、制造实践和其它设计因素。在分流板材料、热电偶放置、加热器产生的热输入和含铅部件处产生的热损失之间存在着一个工程平衡。
赫斯基热流道提供极高水平的热均匀性,其特性包括:
- 经优化的热力设计:分流板基于工程原理,遵循严格的指导方针设计而成。采用热有限元素分析(FEA)对每个分流板设计进行分析。针对每个应用,对热输入、热损失和温度曲线进行优化。
- 经验证的制造设备和过程检查:分流板加热器制造和安装设备是自动化的,实施过程检查以验证精准的加热器元件位置。
- 热均匀性检查:所有成品热流道和分流板系统都在最终装配阶段进行量测和热测试。在装运前,根据合规指导对温度曲线进行审核,一般使用热成像进行审计和故障排除。
热均匀性亟需控制
热力呈均一表现的硬件系统与其控制器的性能息息相关,这往往依赖于精确的温度信号、优化并受控的算法以及快速的反应时间。首要的、同样也是最重要的考虑因素是:用来决定模具温度的热电偶信号的准确性。控制算法的有效性取决于其计算所依据的数据的准确性。如果温度测量因热电偶线路上的高压漏电而受干扰,甚至中断,那么此刻的温测值将被误认作正确的读数,而实际上并非如此。赫斯基Altanium®模具控制器利用隔离的热电偶输入信号,消除了电噪声的影响,并确保温度信号真实有效。
第二个控制部件则是控制算法。该算法包含相关指令——基于热电偶的反馈,调制功率输出以适应过程中的变化。以Altanium控制器为例,该过程采用主动推理技术(ART)进行管理,ART根据特定的操作环境,自动地优化对于每个加热器的控制。
最后的控制部件是反应时间。这一点很重要,因为基于算法的计算一旦执行,处理命令所耗时间越长,温度超出公差范围就越多。使用分布式控制体系结构减少了信号必须传输的距离,从而使命令能够在尽可能短的时间内予以执行。
在分布式体系结构中,温度控制和功率开关电路集成在同一个卡上。温度控制算法直接在线路板上执行,极尽可能地缩短反应时间。操作员界面的主要功能是向卡发送配置参数,并对其进行监控。结果必然是尽可能精准,且可重复性强的温度控制。
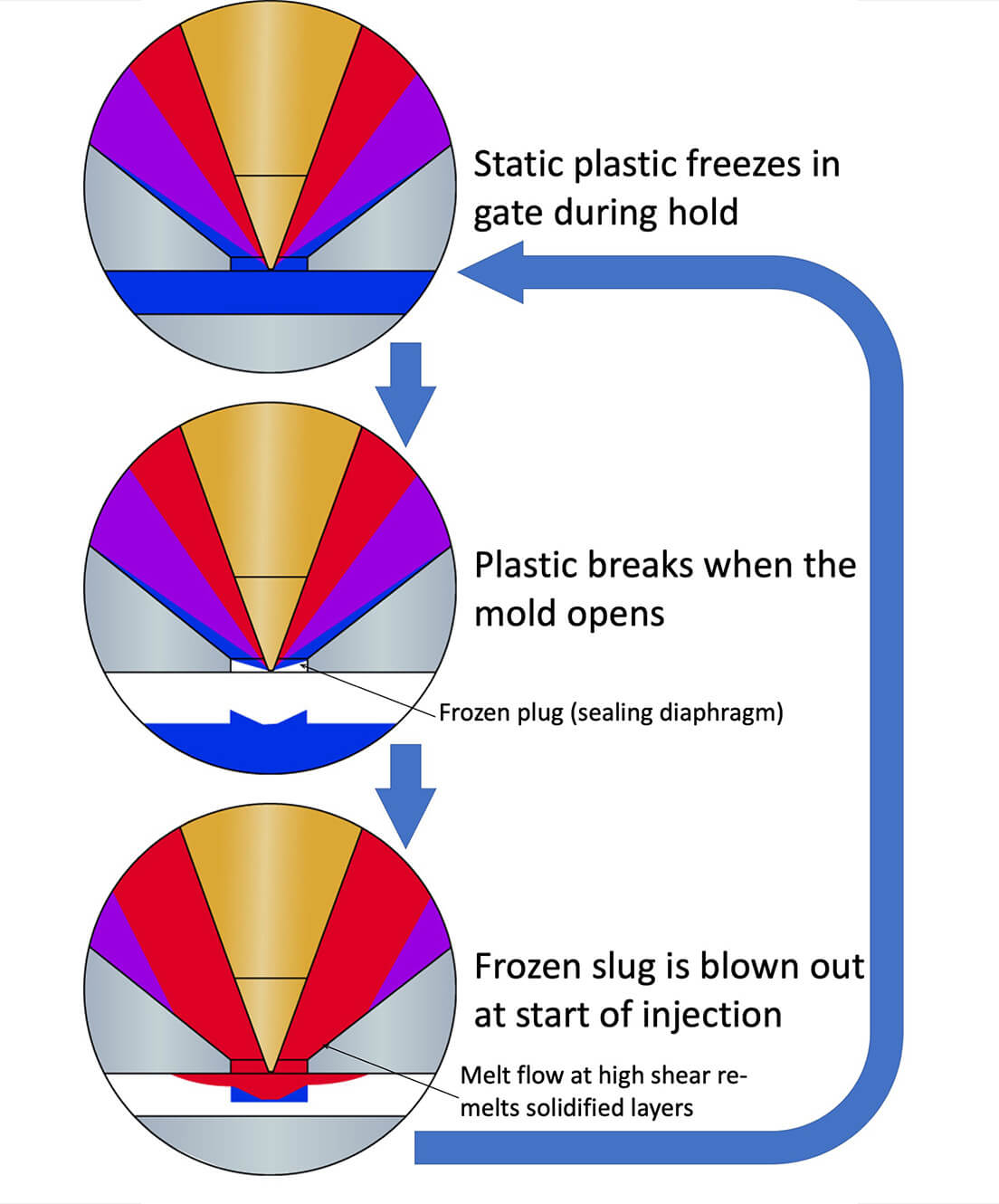
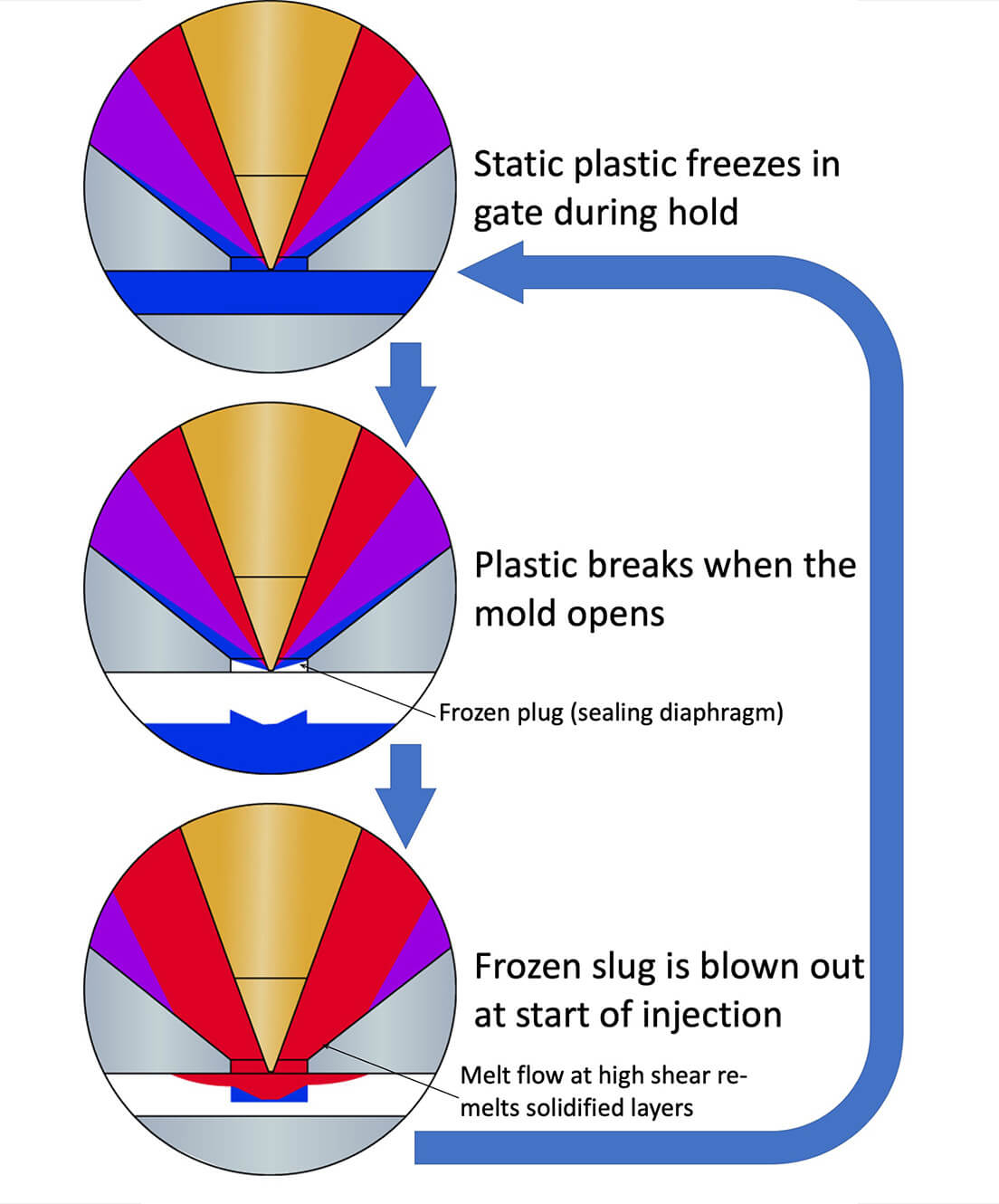
浇口选项发挥主要作用
浇口起限制的作用,塑料通过浇口进入腔位。当前,热点式浇口(热)和阀针式浇口(机械)是热流道浇口的两大选择。在保压期间,塑料在浇口处凝结并形成一层膜或表皮;当模具打开时,这层膜从部件上脱落。留在浇口上的凝结塞在下一个生产周期开启时被吹出。几个浇口间的这种“吹塞”活动的顺序可能是随机的,这可能显现出不平衡,在模具腔位数极高的情形下尤甚。这是由工差导致腔位间和浇口间的细微变化影响所致。即便所供应的树脂本身也并非真正的均质,其分子量在一定范围内不尽相同。可以通过调整热流道温度设定值来减少这些对平衡性所产生的影响。
另一种浇口选择,即阀针式浇口,是一种机械性的控制方式,确保浇口品质更佳。相较之热点式浇口,其提供了更好的注射一致性,得益于机械式的浇口开合规避了热点式浇口所产生的不一致性。除却没有浇口残留问题之外,浇口直径更大,因而浇口剪切力更小,部件的应力也减小。
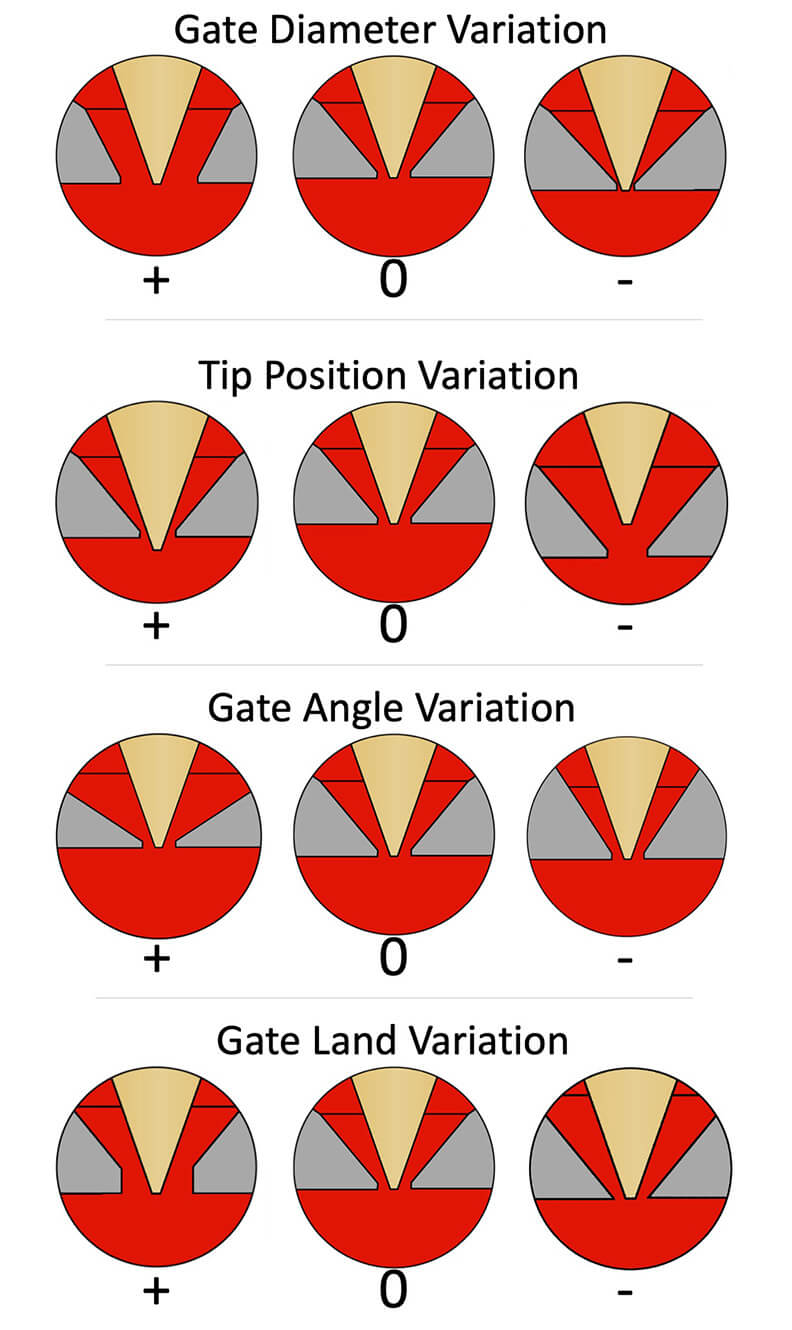
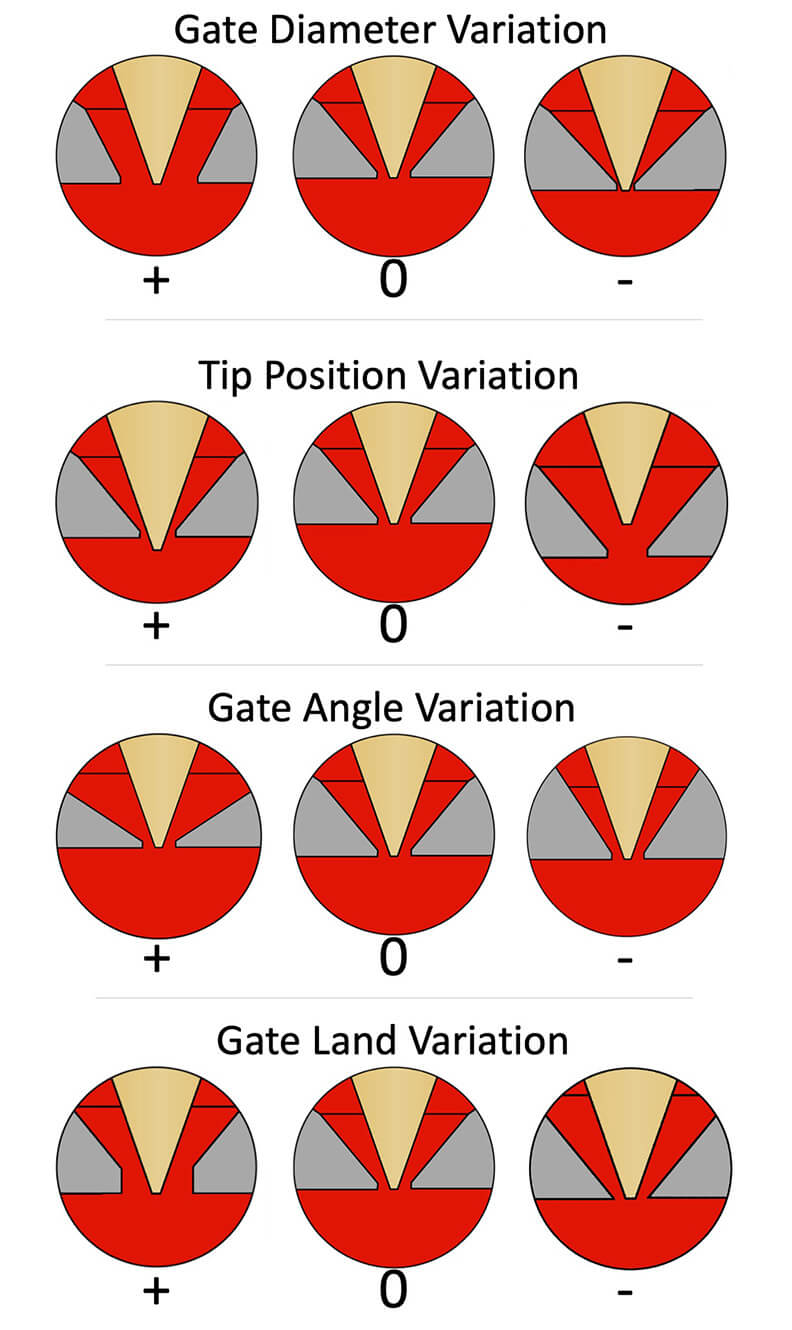
当流体前端到达填充末端时,型腔内压力不断增加,有助于均衡型腔之间的流动平衡差异,使之相等。部件的某些特征也可能对平衡性产生同样的影响,也可能不在填充末端处。例如,瓶盖上的防盗条可能“阻塞”或“计量”流经部件该区域的流量。在这种情况下,最好在这些特性发生作用之前运行故障排除程序。
就填充比率而言,平衡性在速度控制和压力控制(V/P切换)之间的过渡点进行评估。一个48腔模具用于制造重量为5克的部件,加工商一般在240克的总注射重量达到90%或95%时评估平衡性。填充比率法是当速度控制向压力控制过渡时识别异常值(部件填充率小于90%)的工具。在过渡点注射不足90%的部件可能存在模塑缺陷。
首件填充法更适合于故障排除,用来调查模塑系统的具体缺陷或问题。过渡点(V/P切换)经设置,使首个填充部件即为最末一个部件重量的理想比率。所有其它部件的重量将小于该首个填充部件。比如,首个填充件是最终部件重量的95%。
加工商在量测其注塑工艺的短射(注射不足)平衡性时,应合理管理他们的期望值。第一步是确定适合自己的程序。赫斯基推荐填充比率法(95%)。下一步,在明确阀针式浇口系统通常比热点式浇口系统提供更佳平衡性的前提下,为该程序设定一个切合实际的期望值。这些期望均宜合理,宜适中,因为其他因素会对变化及最终的短射(注射不足)平衡性产生不利影响。
如果资质不足的模具超越这些期望值,流程应当继续。调查结果,如果问题未被识别,记录结果并继续进行资质认证。如果存在问题(例如:尺寸问题),应当完成以故障排除为目的的平衡性研究,从而寻找关联因素。
在一个144腔热点式浇口系统的案例中,两个污染问题得到解决。平衡性从67%提高到85%,最终提升至93%。另一个案例中,对平衡性影响最大的因素则是模具的冷却水压力。
短射(注射不足)平衡性测试仅代表一个确认步骤,将变化测量归因于模具,这一点应当为大家所理解。它并未对整体热流道的设计、建造和功能作出任何负面判断。
结论:
短射(注射不足)平衡性在优化注塑工艺中起着重要作用。平衡性量测的最重要的目标之一是通过测量部件重量,从而尽可能减少型腔间的变化。短射(注射不足)平衡性量测是一个重要的评估工具,可在模具资质认证中得以使用,以解决具体问题。用于检查短射(注射不足)平衡性的程序不尽相同,即便对同一系统进行检测,其结果也并非如出一辙。选择适合具体加工需求并匹配期望值的最佳程序极为关键。
诸多要素影响着某个特定模具的短射(注射不足)平衡性能。解决模塑系统的不平衡问题,需要特别地着眼于造成变化的影响因素。减少工艺变化涉及到整个加工系统方方面面的改善。热流道会对短射(注射不足)平衡性产生重大影响;这是模具资质认证中最为常见的考量因素之一。赫斯基优化影响要素,以期尽可能地减少变化,并提高一致性,包括100%几何学平衡的热流道系统设计,具备精确温控性能的热均匀热流道,以及借助赫斯基UltraSync技术消除浇口开合变化。